An Overview of Alkyd Resins
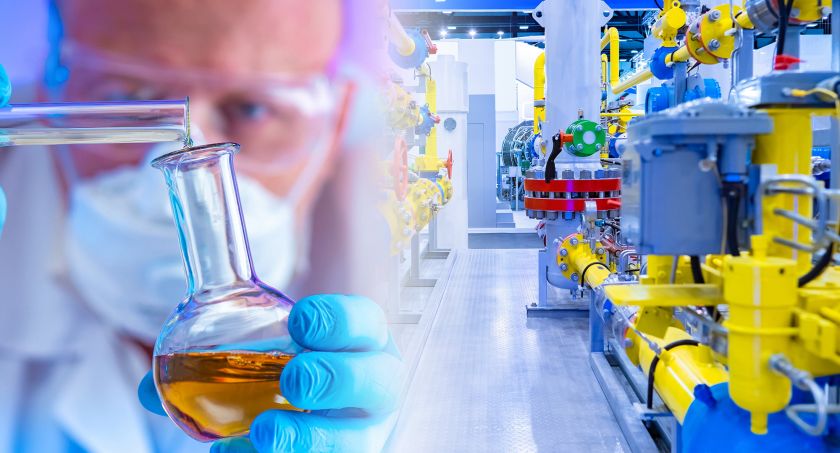
Alkyd-based paints have been a dominant product in the protective coating market since the 1930s. Although they have been challenged by comp
Alkyd-based paints have been a dominant product in the protective coating market since the 1930s. Although they compete with water-based coatings such as latex and acrylics, their unique properties still make them a preferred coating for many applications. They produce a durable, tough, high-quality finish with excellent barrier properties and water resistance. Their strong adhesion to nearly every surface and their resistance to environmental factors make them a preferred coating for machinery, architectural, industrial and wood applications. Easy-to-use formulations of alkyd-based paints make it possible to apply them without special mixing or complex application equipment. Most formulations are applied with a brush, roller or aerosol spray.
Although they are more expensive than latex and acrylic paints, their performance advantages and ease of application have allowed them to maintain a significant market. While the original solvent-borne formulations have been challenged in the market because of environmental restrictions, newer waterborne alkyd coatings and modified alkyd coatings provide the high performance of the solvent-borne products with highly reduced solvent content. The use of vegetable oils rather than petroleum-based oils also gives alkyds a unique opportunity as a green product.
Though it once appeared that the environmental challenges of solvent-based alkyds would severely limit the use and commercial viability of alkyd coatings, the industry has responded with newer waterborne, low-VOC products that provide the high performance of oil-based paints while addressing the environmental concerns of the older, traditional solvent-borne coatings. With these advances, alkyd coatings will remain a dominant player in the protective coatings market.
Alkyd paints are relatively easy to use. They are supplied to the market as one-pot products, requiring no mixing other than stirring prior to use to ensure uniform distribution of the pigments and additive. Most alkyd paints are applied with an applicator, such as a brush or roller, or as an aerosol spray. The aerosol application method can be through a compressed-air spray gun or formulated for an aerosol spray can.
The typical application should use thin coatings to allow the oxidative curing to occur. Thick coatings can form a surface skin, leaving an uncured liquid component below the surface. Where thicker coatings are desired, it is recommended that several thin layers be applied rather than one thick layer.
The drying time for an alkyd coating varies depending on the oil length, oil type and environmental conditions. For short oil alkyds, which produce a harder surface, heat is usually required for effective drying.
Although solvents can be used to thin the paint, care must be taken because solvents will affect the viscosity and drying time of the coating.
When stored for long periods, the components in alkyd paint can settle, leaving a non-uniform distribution of the paint components. For this reason, it is recommended that the paint be boxed prior to use.
As with all paint products, the best results are obtained when the instructions on the container are followed, because these instructions are specifically designed by the manufacturer for the formulation of that specific product.