冷镀锌(冷涂锌)涂料的发展应用
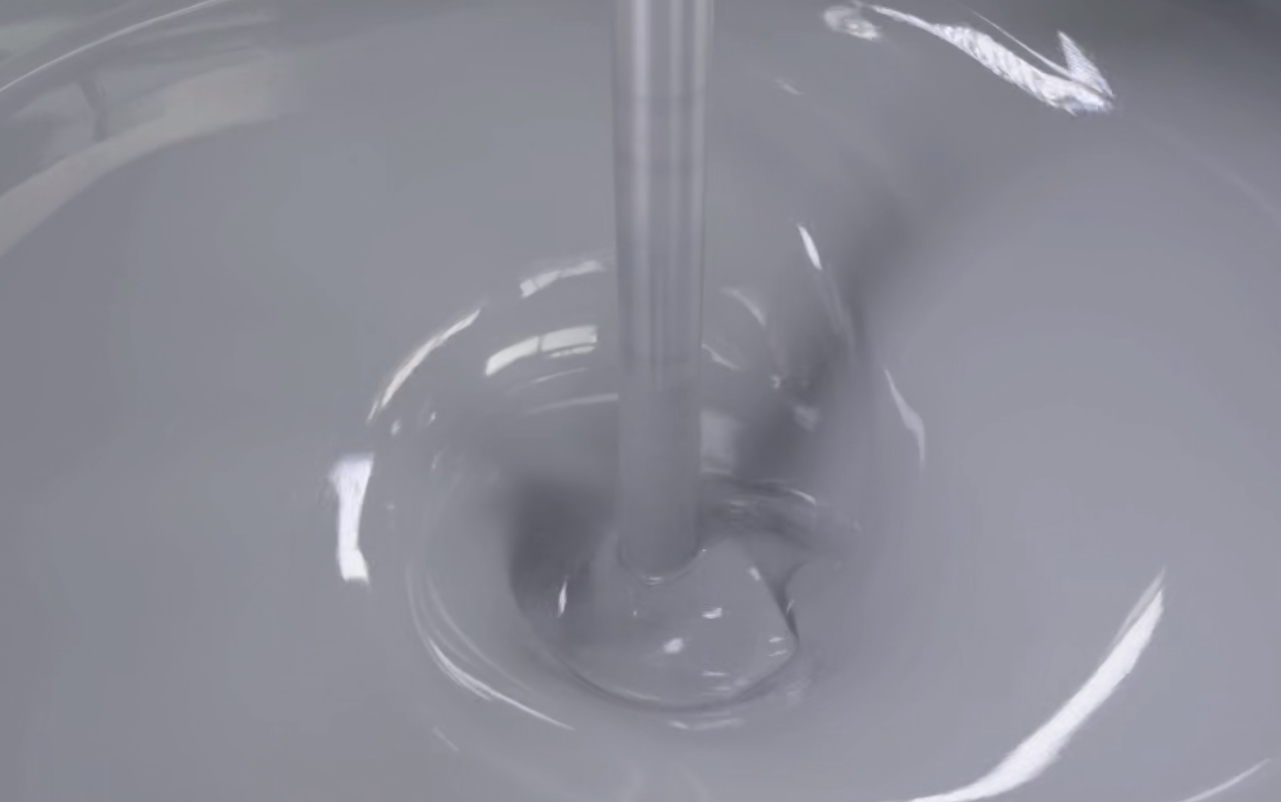
一种高锌含量的单组分有机涂料,与热浸镀锌或热喷锌层有着相同保护效果,主要用于钢材表面的阴极防护,以及对镀锌或喷锌层破坏的修补。
冷镀锌(冷涂锌)涂料的定义
冷镀锌(冷涂锌)涂料,由超细锌粉、导电包覆树脂以及有机挥发溶剂组成。最早从国外引入中国时,因为其有着与热浸镀锌相同的的保护效果,又称为冷镀锌;与热喷锌也有着相同的保护效果,又被称为冷喷锌。国内也有一些厂家称之为锌加等。
统一冷镀锌(冷涂锌)涂料行业标准,明确冷涂锌概念,避免与富锌涂料混淆,对促进行业技术进步,引导行业健康,有序发展具有重要意义。全国涂料与颜料标准化技术委员会于2014年开展了冷涂锌涂料标准的制定工作,2016年1月1日正式颁布 实施HG/T 4845–2015。该标准规定了冷涂锌涂料的要求,试验方法等,适用于常温施涂的高锌含量的有机涂料,主要用于钢铁底材暴露表面的阴极防护,及镀锌层或喷锌层破坏的修补。该标准不适用于多组份富锌底漆。
桥梁标准JT/T1266-2019 电力标准T/CSEE0103-2019
冷镀锌(冷涂锌)涂料可以定义为:一种高锌含量的单组分有机涂料,与热浸镀锌或热喷锌层有着相同保护效果,主要用于钢材表面的阴极防护,以及对镀锌或喷锌层破坏的修补。
冷镀锌(冷涂锌)涂料与富锌涂料(Zinc Rich Coating)的区别在于锌粉含量。通常重防腐涂料中常用的环氧富锌或无机富锌涂料,按照ISO 12944的要求,干膜中的锌粉含量至少要达到80%。冷涂锌中的实际锌粉含量高达96%,这也是两者最大的区别。冷涂锌为单组份产品,环氧富锌和无机富锌是双组份产品。
冷涂锌的发展
在20世纪50年代,英国剑桥大学的学者提出了冷涂锌概念,即“热镀锌的常温化”,并在20世纪60年代由英国、美国等国开始研发。
最初冷镀锌(冷涂锌)仅被认为是富锌涂料的性能增强,研究重心仅是研发与锌粉附着能力更好的树脂。1972年,达克罗技术的第一个实用专利申请成功并迅速实现工业化大规模应用。尽管达克罗与冷镀锌(冷涂锌)涂料是两种完全不同的技术,但是其应用给尚处于初级阶段的冷涂锌技术带来了新的思路。同年,冷镀锌(冷涂锌)树脂技术取得进展。1975年,瑞士研发出第一款真正意义上的冷镀锌(冷涂锌)产品,开创了世界上直接喷出金属的历史,该产品干层锌含量约为93%,符合欧洲DIN50.976(1980)所述的阴极防腐性能标准,从此冷涂锌逐步获得发展和应用。
近30年来,冷涂锌涂料发展迅速,最终被定义为干膜锌含量高于95%,以阴极保护为主的单组分涂层,并从富锌涂料种类中分离出来。
在我国的行业标准规范HG/T 4845–2015中,冷镀锌(冷涂锌)涂料中锌粉含量必须高于95%。实际的冷涂锌产品中,比利时锌加(ZINGA),日本罗巴鲁(ROVAL)、美国ZRC等,上海的昊锌(HAOXIN)等,锌粉含量都在96%以上。
我国冷镀锌(冷涂锌)涂料研发、生产、应用起步较晚,前期主要是少数国外公司的产品在国内有零星应用,最早进入中国市场的是比利时的“锌加”(ZINGA)和日本“罗巴鲁”(ROVAL)的产品。在2005年左右,我国的冷涂锌涂料技术开始得到发展,并逐步应用于恶劣环境下的钢结构防腐,包括电力工业(图1)、桥梁、水利枢纽、海洋平台、机场、交通轨道钢结构,以及混凝土钢筋等等。
冷镀锌(冷涂锌)涂料的防腐蚀机理
冷镀锌(冷涂锌)涂料产品的树脂,是独特的有机导电树脂。普通涂料产品的树脂,例如环氧富锌涂料的环氧树脂,并不具备导电性。而冷涂锌产品的有机导电树脂,使锌粉之间形成了导电网链,树脂将锌粉均匀包覆并形成导电通道,使电子可沿着相互接触的粒子进行传递而使整个涂膜具有导电性。
冷镀锌(冷涂锌)涂料涂层干膜中含锌量高达96%,远远大于传统的富锌涂料中的锌粉含量。高含量锌粉带来优异的阴极保护性能,防腐蚀性能优于富锌涂料,相同于热浸镀锌和热喷锌涂层对钢材的保护。
国家标准GB/T 6890-2012锌粉中规定了不同等级的锌粉化学成分,且于冷涂锌的锌粉必须达到最高等级一级锌粉的要求,即主品位全锌含量不得低于96%,金属锌含量大于92%。实际上优质冷涂锌所用的锌粉原材料,全锌大于99%,金属锌大于97%。
冷镀锌(冷涂锌)涂料产品选用的锌粉,必须采用的超高纯度锌粉。超高纯度的锌粉,避免了由于铁、铅、镉等杂质存在而形成微电池,杜绝了镀层产生麻点腐蚀,有利于镀锌层对钢铁基体的保护。
GB/T 6890规定的锌粉等级见表1。标准中规定的铅杂质含量不大于0.1%,铁杂质含量不大于0.05;冷涂锌产品中使用的锌粉产品的品质,铁杂质要求为0.005%,检测值仅为0.0003%数量级;铅杂质含量要求为0.01%,实测值不高于0.005%。
锌粉的细度对冷镀锌(冷涂锌)涂料产品有着至关重要的影响,表1为标准所规定的锌粉细度等级,共分为四级。其中最高等级FZn30最大粒径不得大于45mm,粒度分布30mm以下的不小于99.%,10mm以下的不小于80%。
冷镀锌(冷涂锌)涂料中实际使用的锌粉,最大粒径要求不大于25mm,平均粒径在3~5mm。
超细粒径的锌粉,使锌颗粒间的接触面大且多,排列紧密空隙小,从而涂层致密,孔隙率低,涂层表面粗糙度低。即使涂膜锌层中存在一定的结构间隙,也可被更细小的锌粉颗粒填充,更加大涂膜的致密度。超细锌粉粒径细小,其表面活性大,促进沉积,有利于锌涂层的形成。图2为冷镀锌(冷涂锌)的涂膜截面图。
采用超细锌粉,可以使用更少的树脂来包覆更多的锌粉,当超过90%时就可以产生很好的阴极保护作用,冷涂锌产品使用了超细锌粉,含量可以达到96%。
中国科学院金属研究所中国科学院核用材料与安全性评价重点实验室的刘福春等,以冷涂锌涂料配方为基础,不同锌粉含量的单组分产品,在(23±3)µm的厚度下,进行的盐雾试验和电化学阻抗谱试验结果果表明,锌粉含量对涂层性能决定性的影响。图2分别为锌粉含量50%、75%、90%和95.2%的产品,在500小时的盐雾试验后的表现,而95.2%锌粉含量的产品未见腐蚀红锈。
优质冷镀锌(冷涂锌)涂料产品干膜含有96%的锌粉,按每微米厚度在每平方米上面7.14g/m2,与热浸镀锌的附着量相比,不同涂层厚度下的锌含量见表3,两者相当接近。
海洋腐蚀与防护国防科技重点实验室的黄国胜等,对冷镀锌(冷涂锌)涂料涂层、热喷锌涂层、纯锌块和Q235钢在海水中腐蚀电位的测试表明,随时间的变化规律,可以看出,各种试样在海水中的自然腐蚀电位非常接近,且电位比较稳定。纯锌的电极电位在-1.0~-1.02V(SCE)之间波动,冷镀锌(冷涂锌)涂料涂层的腐蚀电位100h后电位基本稳定在-1.0V(SCE)。热浸锌锌层的腐蚀电位变化规律与冷镀锌(冷涂锌)涂料涂层的腐蚀电位变化规律类似,100h后电位基本稳定在-0.98V(SCE)。Q235钢的腐蚀电位在浸泡600h后维持在-O.69V(SCE)左右,钢的最小保护电位为-0.78V(SCE)。可以看出,冷镀锌(冷涂锌)涂料涂层和热浸锌锌层一样可以给钢铁基体提供足够的阴极保护驱动电位,说明冷镀锌(冷涂锌)涂料涂层与热浸锌锌层有着相同的保护效果。
湖南林业大学的杨焰等对冷镀锌(冷涂锌)涂料进行了研究。冷镀锌(冷涂锌)涂料、热浸镀锌与裸钢在3%NaCl溶液中的极化曲线特征值见表4,表明冷镀锌(冷涂锌)与热镀锌的腐蚀电位至少比裸钢电位高400mV。在腐蚀介质中,两种涂层均能为钢基体提供阴极保护驱动力,冷镀锌(冷涂锌)和热浸锌涂层的腐蚀电流均高于裸钢,说明裸钢基体上的含锌涂层产生了阴极电流,起到阴极保护作用。因此,由于两种含锌涂层的电化学保护作用,裸钢腐蚀被抑制,涂层起到保护作用。冷镀锌(冷涂锌)和热浸锌涂层具有相似的腐蚀电位与腐蚀电流密度,当冷镀锌(冷涂锌)与热浸锌涂覆在裸钢基材上时,冷镀锌(冷涂锌)能达到与热浸锌相似的防腐蚀效果。
传统的防腐蚀涂料,主要以屏蔽型为主。当漆膜破损或老化失去保护作用时,就失去了保护作用,外界的腐蚀因子就会使钢铁腐蚀,锈蚀会从涂膜破损处蔓延至涂层完处的下面,导致涂层大面积脱落,失去保护效果。冷镀锌(冷涂锌)涂层具有很强的电化学保护作用。特殊有机树脂在锌颗粒的周围形成了致密的保护屏障层,可抵御外界的侵蚀。同时在涂膜锌层表面,锌颗粒产生的各类锌盐,填满了涂层的孔隙,形成了一层锌盐屏障,减缓了镀锌层和钢结构的腐蚀速率,从而延长保护期。在涂层受到破坏时,锌层能起到电化学保护作用,使露出的局部钢材表面受到电化学保护作用而不受到腐蚀,同时产生的锌盐能填充进涂膜受损处起到一定的保护作用。即使锌层破坏较为严重,锌层下的钢材也不会受到周边腐蚀的影响,不会产生锈蚀。传统的一般涂料与冷涂锌涂料不同的保护作用,见图5。